Welcome To Varun Packaging
We take pride in introducing ourselves as one of the country's leading manufacturers of corrugated boxes and unit boxes. In fact we specialize in providing total packaging solutions.










Our Services
We are fully equipped to manufacture and deliver various types of corrugated boxes.
As per the client's requirements. Some of the products we specialize in are :
Master Cartons
This Cartoon Box is largely demanded in water houses and cold storage for packaging sweets, tea, bottles and food items. This product is designed by our trained professionals using premium quality material and latest techniques.
Corrugated Pallets
Corrugated pallets are a lightweight but highly durable alternative to wooden pallets. Made from heavy-duty corrugated cardboard, they are designed to withstand the demands of your entire supply chain.
Shipping Containers
For many companies and organizations, a "shipping container" is a box you saved from a shipment you received with the label peeled off or crossed out, and a new shipping label applied. If this is how you ship out your products, you're missing out on some important benefits custom shipping boxes can provide.
Die Cut Items
Die cut boxes are highly customizable corrugated cardboard boxes designed to fit any shape, size, or need. They are known as die cut boxes because they are cut from plain sheets of corrugated material on a machine known as a die press (or die cutter).
Interior Packaging
Packaging Boxes are seen by the end users, hence they need to be attractive and convenient to open. We are offering interior packaging box, point of purchase packaging box, ring flaps, boxes with foldable flaps etc.
Printed Boxes
We provide a range of printed corrugated shipping boxes are manufactured from good quality fiber material. We use excellent qualities of material in manufacturing of these printed corrugated shipping boxes so it is easily carried anywhere.
What we do
- Pulping the pine chips
(1) Manufacturing a corrugated cardboard box begins with the pulping of wood chips in the kraft (sulfate) process. First, tree trunks are stripped of bark and torn into small chips. Next, these chips are placed in a large, high-pressure tank called a batch digester, where they are cooked in a solution, or liquor, made of sodium hydroxide (NaOH) and several other ionic compounds such as sulfates, sulfides, and sulfites. These strongly alkaline chemicals dissolve the lignin, the glue-like substance that holds the individual wood fibers together in a tree trunk.
(2) When the pressure is released after several hours, the wood chips explode like popcorn into fluffy masses of fiber.
- Making kraft paper
(3) After additional cleaning and refining steps, a consistent slurry of wood pulp is pumped to the paper-making machine, also known as a Fourdrinier machine. Gigantic, square structures up to 600 feet long (182.88 meters), these machines contain a wire mesh in which the paper is initially formed. Next, the paper is fed into massive, steam-heated rollers and wide felt blankets that remove the water. At the end, the finished medium, or liner, is rolled for shipment.
- Shipping and storing the kraft paper
(4) Rolls of kraft paper for corrugating are available in many sizes to fit the production equipment at different corrugating plants. The most common roll sizes are 67 inches (170.18 centimeters) wide and 87 inches (220.98 centimeters) wide. An 87-inch roll of heavier paper can weigh up to 6,000 pounds (2,724 kilograms). As many as 22 rolls of 87-inch paper can be loaded into one railroad boxcar for shipment to a corrugating plant.
(5) At the plant, the kraft paper is separated into different grades, which will be used for the medium and the liner. These different grades of corrugated cardboard can be made by combining different grades of kraft paper. A knowledgeable packaging specialist works with a customer to determine the strength required for the corrugated cardboard container being planned. Then, when a plant receives an order for containers, a product engineer specifies the combination of medium and liner to produce a cardboard to match the customer's requirement.
- Corrugating the cardboard
(6) Using powerful fork-lifts, skilled equipment operators select, move, and load rolls of kraft paper at one end of the corrugator.
(7) One roll of medium is loaded to run through the corrugating rolls, and a roll of liner is fed into the corrugator to be joined with the corrugated medium. Liner from another roll travels up over the corrugating rolls along a flat structure called the bridge. This liner will be glued to the corrugated medium later in the process.
(8) For a large production run, additional rolls are loaded into automatic splicers. Sensitive detectors check the rolls of paper feeding into the corrugator. When a roll is nearly empty, the corrugator control system starts a splicer, and paper from the new roll is joined to the end of the paper going through the machine. Thus, production of corrugated cardboard is continuous, and no production speed is lost.
(9) The medium to be corrugated is fed into the giant, electrically driven rollers of the corrugator, first through the preheating rollers and then into the corrugating rolls. Steam at 175 to 180 pounds of pressure per square inch (psi) is forced through both sets of rollers, and, as the paper passes through them, temperatures reach 350 to 365 degrees Fahrenheit (177 to 185 degrees Celsius).
(10) The corrugating rolls are covered with I O flutes —horizontal, parallel ridges like the teeth of massively wide gears. When the hot paper passes between the corrugating rolls, the flutes trap and bend it, forming the middle part of a sheet of corrugated cardboard. Each corrugating machine has interchangeable corrugating rolls featuring different flute sizes. Installing a different A finished piece of corrugated cardboard consists of a single corrugated layer sandwiched between two liner layers. A finished piece of corrugated cardboard consists of a single corrugated layer sandwiched between two liner layers. flute size in the corrugator changes the width of the corrugated medium.
(11) The medium travels next to a set of rollers called the single-facer glue station. Here, one layer of liner is glued to the medium. Starch glue is carefully applied to the corrugated edges of the medium, and the first layer of liner is added. From the single-facer, the medium and liner go to the double-backer glue station where the other layer of liner from the bridge is added following the same procedure. Continuing through the corrugator, the cardboard passes over steam-heated plates that cure the glue.
- Forming the blanks into boxes
(12) At the end of corrugator, a slitter-scorer trims the cardboard and cuts it into large sheets called box blanks. Box blanks pop out of the slitter-scorer like wide slices of toast and slide into an automatic stacker that loads them onto a large, rolling platform. From here, they will be transported to the other machines that will convert them into finished containers. Skilled production workers use a computer terminal and printer to prepare a job ticket for each stack of box blanks produced by the corrugator. With the job ticket, workers can route the stack to the right fabrication machines, called flexos (the name is short for flexographic machine). A flexo is a wide, flat machine that processes box blanks.
(13) Printing dies and die-cutting patterns I 3 are prepared in a pattern shop on large, flexible sheets of rubber or tin. The dies and patterns are loaded onto the large rollers in the flexo, and the box blanks are automatically fed through it. As each blank passes through the rollers of the flexo, it is trimmed, printed, cut, scored, and, in a printer-folder-gluer, folded and glued to form a box. From the flexo, the finished boxes are automatically stacked and sent to a banding machine to be wrapped for shipping. Other equipment in a corrugating plant includes stand-alone die-cutters, die-cutters with print stations, and machines known as curtain coaters that apply a wax coating to fruit, vegetable, and meat containers. Box blanks requiring only simple, one-color printing and die-cutting can be run through a stand-alone die-cutter, print station, and curtain coater to produce water- or grease-resistant containers.
clients Testimonial
Rajat Gupta
I have to say that Varun Packaging offers excellent products and very good prices.Keep up the good work.
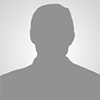
Shivkripa Ent.
Superfast shipping with good quality items at reliable price.They have provided materials in time.
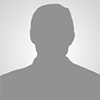
Raju Mishra
I was looking for packing materials and i found V.P. They are very good,and they have wider product lines.
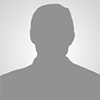
Kamal Yadav
Thank you for arranging the material in such short while. We appreciate courtesy and support.
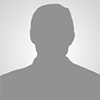